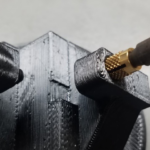
Liberty Electronics : Leader de l’innovation grâce à l’Impression 3D Stratasys
Fondée en 1985, Liberty Electronics est une entreprise de premier plan spécialisée dans la conception et la fabrication de faisceaux de câblage électronique, d’assemblages de câbles, d’armoires complètes et de panneaux, ainsi que d’assemblages électromécaniques. Son unité commerciale spécialisée dans le secteur militaire et aérospatial, basée à Franklin en Pennsylvanie, se distingue par ses investissements dans l’impression 3D et la création de prototypes pour rester à la pointe de la fabrication.
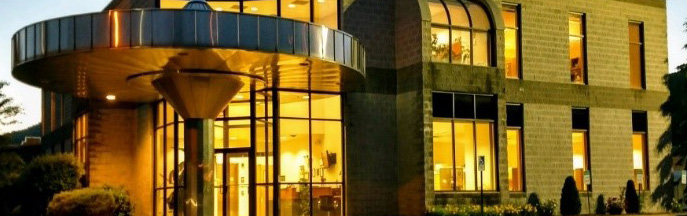
Le défi
Liberty Electronics s’appuie sur des gabarits spécifiques pour la production de divers composants électroniques. Ces gabarits doivent être robustes, capables de dissiper les charges électrostatiques (ESD), et résistants à la chaleur ainsi qu’aux produits chimiques. Un exemple particulier concernait un gabarit conçu pour monter et fixer précisément un condensateur en céramique et un capteur de température lors d’un cycle de durcissement à haute température d’une époxyde structurale. Ce gabarit devait non seulement résister à la chaleur, mais aussi fournir une protection ESD à l’ensemble électronique. La pièce pouvait être usinée, mais cela nécessitait un traitement post-usinage pour garantir la conformité ESD et les délais étaient plus longs que souhaité.
La solution
Plutôt que d’usiner le gabarit en aluminium 6061 et d’ajouter une post-traitement pour les propriétés ESD, Liberty Electronics a choisi de l’imprimer en interne avec le thermoplastique PEKK Antero™ 840CN03 sur son imprimante 3D Fortus 450mc™. Le matériau Antero 840CN03 a parfaitement répondu à toutes les exigences de solidité, de résistance à la chaleur et de capacité ESD, tout en offrant les avantages suivants :
– Réduction significative du temps de production
– Coûts de matériaux plus bas
– Peu ou pas de post-traitement grâce à une excellente finition de surface
– Conformité ESD
De plus, la fabrication additive a permis d’ajouter des inserts métalliques en post-production.
L’impact
La production interne du gabarit grâce à la fabrication additive FDM® et au matériau Antero 840CN03 a réduit le délai de fabrication de deux semaines à deux jours, soit un gain de temps de 86 % par rapport à l’usinage externe de la pièce en aluminium 6061. En interne, cela a également permis une économie de coûts de 89 %.
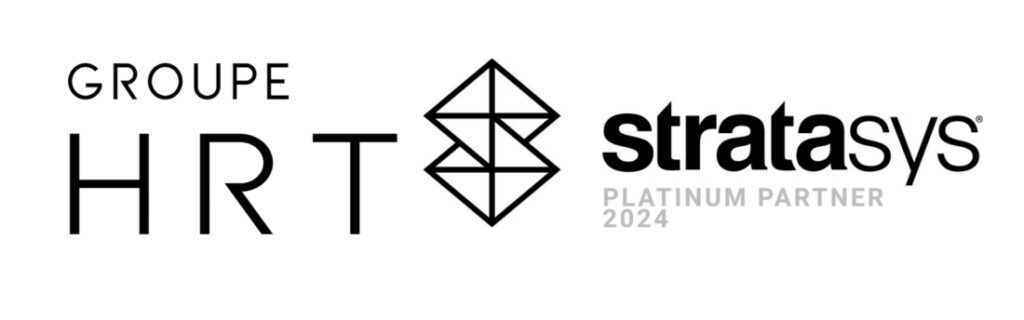
Si vous aussi souhaitez révolutionner vos processus de fabrication avec des solutions d’impression 3D avancées, contactez notre équipe dès aujourd’hui. En tant que partenaire Platinium Stratasys, nous vous offrons un accès privilégié à la meilleure technologie d’impression 3D du marché pour répondre à vos besoins industriels.