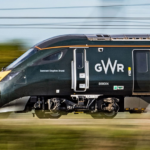
Comment GWR utilise l’impression 3D pour promouvoir la durabilité ferroviaire
Comment accélérer la transition du transport ferroviaire à base de combustibles fossiles vers un modèle électrifié plus respectueux de l’environnement ? Great Western Railway (GWR) au Royaume-Uni pense avoir trouvé une solution grâce à l’impression 3D.
Une alternative plus écologique pour le transport ferroviaire
GWR est une compagnie ferroviaire opérant dans le sud-ouest du Royaume-Uni. En tant qu’innovateur majeur dans l’industrie ferroviaire, la société est à l’avant-garde du seul train à batterie à charge rapide du pays, en convertissant d’anciens wagons destinés à la casse. Une grande partie du réseau ferroviaire britannique n’étant pas électrifiée par des câbles aériens standards, l’alternative actuelle reste les trains diesel coûteux et polluants. Cependant, avec une approche créative en faveur de la durabilité des transports, GWR transforme d’anciennes rames de la ligne District de Londres en unités modernes à batterie électrique.
Bien que les lignes électrifiées restent la référence en matière de transport ferroviaire électrique, le développement de cette infrastructure est souvent lent. « C’est très coûteux et logistiquement compliqué. Avec ces deux paramètres, il devient difficile de faire avancer les choses », explique Julian Fletcher, responsable du développement technique chez GWR. « C’est là que les trains à batterie entrent en jeu. Ces dernières années, la technologie des batteries les a rendus viables, et la technologie de charge rapide les rend maintenant pratiques pour des lignes secondaires plus courtes », ajoute Fletcher.
Cela signifie que des trains à batterie à charge rapide, comme sur la ligne Greenford-West Ealing au nord-ouest de Londres, permettront au Royaume-Uni de décarboner plus rapidement les lignes de banlieue. Cela est d’autant plus important que l’énergie électrique des batteries offre un coût par kilomètre inférieur à celui des alternatives à hydrogène ou diesel, tout en améliorant la qualité de l’air.
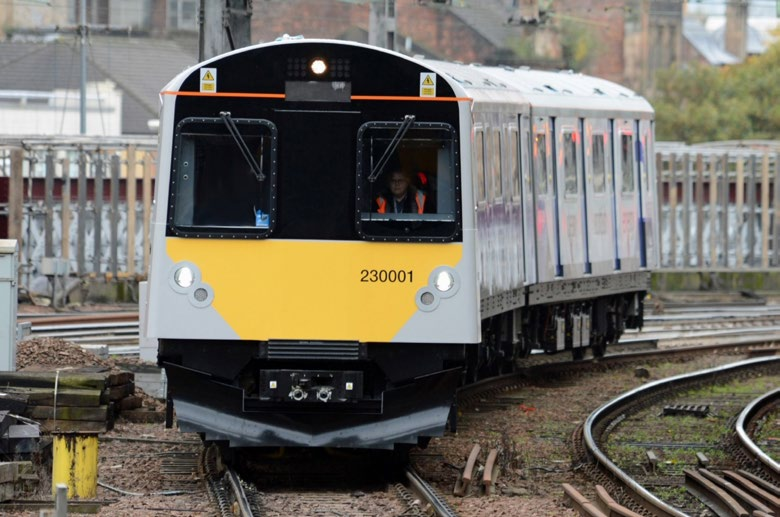
La recharge rapide permet aux trains de circuler sans interruption
Le train à batterie de GWR peut suivre un emploi du temps quotidien complet et faire face à des situations d’urgence, mais il doit être rechargé à un moment donné. Pour cela, GWR a développé un ingénieux système de recharge rapide « rail et chaussure » qui permet de recharger les batteries pendant que le train est à la station. Lorsque le train entre dans la station, l’ensemble de la chaussure est abaissé et se connecte aux rails conducteurs à l’arrêt du train. Ces rails fournissent ensuite de l’électricité à partir de batteries situées sur le bord des voies, permettant de charger rapidement le train en seulement 10 minutes.
Cependant, la réalisation de ce design innovant n’a pas été sans difficultés. Des protections étaient nécessaires pour protéger les composants de la chaussure, mais les restrictions d’espace sous le train ont compliqué leur conception. « Nous ne pouvions pas les fabriquer en acier plié, et le moulage était hors de question dans les délais impartis. L’impression 3D industrielle était donc vraiment la solution », explique Fletcher. Les propriétés de haute résistance et de résistance au feu de la résine ULTEM™ 9085 ont constitué un choix de matériau approprié. La liberté de conception offerte par l’impression additive a également permis aux ingénieurs de GWR d’exploiter l’espace disponible sous le train pour placer les capteurs de la chaussure.
Le train est conçu pour fonctionner dans les hivers rigoureux britanniques et les étés de plus en plus chauds. Grâce aux données de test de matériaux étendues de Stratasys disponibles pour la résine ULTEM™ 9085, GWR a pu obtenir toutes les spécifications de performance mécanique nécessaires dans une plage de températures allant de -54 °C à 149 °C. Associées aux données sur les normes de sécurité incendie ferroviaire européennes EN 45545-2 de Stratasys, les ingénieurs de GWR étaient convaincus que le matériau répondait à toutes leurs exigences.
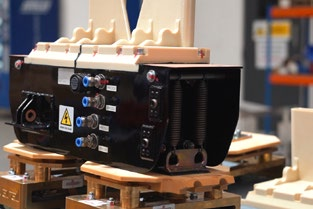
Preuve de la polyvalence de l’impression additive
Un exemple éclatant de l’un des principaux avantages de l’impression additive est sa diversité d’application. Elle offre aux ingénieurs les outils nécessaires pour trouver des solutions économiques et efficaces en termes de temps pour une grande variété de problèmes. Cela se manifeste dans la capacité de GWR à utiliser l’impression 3D pour plusieurs cas d’utilisation afin de préparer le train à son emploi du temps inaugural dans un délai extrêmement court.
En plus des couvercles de la chaussure de recharge, il y avait également un besoin de remplacer le tableau de bord du conducteur. La pièce d’origine était un moulage en aluminium, mais la pièce de remplacement était affectée par des problèmes de porosité et d’autres défauts de finition, entraînant de graves retards dans la préparation opérationnelle du train.
Les ingénieurs de GWR ont contacté Stratasys pour obtenir un tableau de bord imprimé en 3D, car les efforts précédents pour trouver une ressource capable d’imprimer de grandes pièces dans des matériaux résistants au feu avaient échoué. En réponse, les ingénieurs d’application de Stratasys ont développé et imprimé un tableau de bord de remplacement sur une imprimante F900®, qui dispose d’un volume de construction suffisant pour produire des pièces de grande taille.
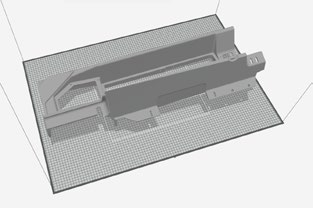
En plus de recevoir la pièce dans un délai de seulement une semaine, les ingénieurs de GWR ont constaté qu’elle était 57 % plus légère que le moulage (3,5 kg contre 8,1 kg) et qu’elle n’avait pas les mêmes contraintes de géométrie que celles que les concepteurs devaient auparavant prendre en compte lorsqu’ils travaillaient avec un moulage. Daniel Jones, responsable de la conception mécanique chez GWR, a noté qu’une fois le tableau de bord peint dans la même couleur que le reste de la cabine, le composant imprimé était presque indiscernable de l’original.
Les matériaux polymères apportent la solution
Les ingénieurs de GWR ont rapidement réalisé qu’en plus des économies de coûts et de poids, le remplacement des composants métalliques par des polymères imprimés en 3D offre des avantages supplémentaires. Par exemple, les trains modernisés sont équipés de conduits et de grilles de climatisation en métal dans le plafond de la cabine. Lorsque l’air frais s’échappe du conduit et rencontre l’humidité croissante du compartiment passager, de la condensation se forme sur la grille en métal, ce qui pourrait entraîner des gouttes sur les passagers. Pour éviter ce problème, des grilles imprimées en 3D en polymère, qui conservent des températures de surface plus élevées, ont été choisies afin de prévenir la formation de condensation.
La conception de la grille utilise deux supports imprimés pour permettre un montage pratique dans les trous existants de l’ancienne conception. Dans le but de garantir une longue durée de vie à ces composants additifs, les ingénieurs de GWR ont intégré des limiteurs de compression qui sont ajustés après impression, offrant ainsi une méthode pratique pour assurer une résistance à la compression suffisante dans les connexions boulonnées en polymère.
Remplacer les anciennes pièces par des alternatives imprimées en 3D
Suite au succès du tableau de bord, les ingénieurs de GWR ont rencontré un problème avec le cadre d’affichage du côté conducteur. Cette fois-ci, un matériau FDM® spécifique a été nécessaire pour répondre aux exigences de transport.
Le portefeuille de matériaux FDM de Stratasys comprend des matériaux validés développés en partenariat avec des fournisseurs tiers tels que Kimya, permettant ainsi de commercialiser plus rapidement de nouveaux matériaux FDM. Pour cette application, les ingénieurs de Stratasys ont utilisé le polycarbonate ignifuge Kimya PC-FR, qui est un matériau adapté aux applications à exigences moindres, offrant une alternative économique aux thermoplastiques plus coûteux. Le résultat a été une pièce de remplacement produite rapidement et à moindre coût par rapport aux alternatives, tout en respectant le niveau de risque d’incendie ferroviaire HL3 le plus élevé.
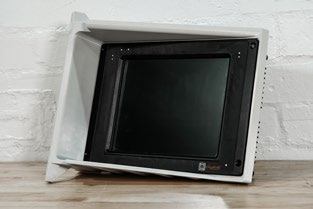
À titre de référence, le tableau 1 compare le matériau validé Kimya et plusieurs autres polymères en fonction de leur capacité à respecter les normes FST (flamme/fumée/toxicité). Il montre l’épaisseur nécessaire de chaque matériau pour passer le niveau de risque d’incendie ferroviaire HL3 de la norme EN45545-2.
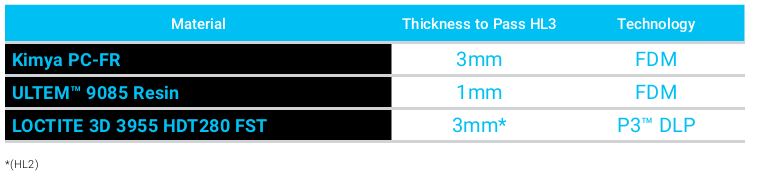
Cependant, les matériaux classés FST ne sont pas toujours nécessaires dans certaines circonstances, et les matériaux Stratasys non classés FST peuvent être utilisés avec succès, comme l’indique le tableau 2. Par exemple, des dérogations peuvent être accordées lorsque le poids de la pièce est inférieur à une valeur spécifique. Les normes EN45545-2 fournissent des informations supplémentaires sur la masse combustible, la surface, la localisation des pièces et le regroupement.
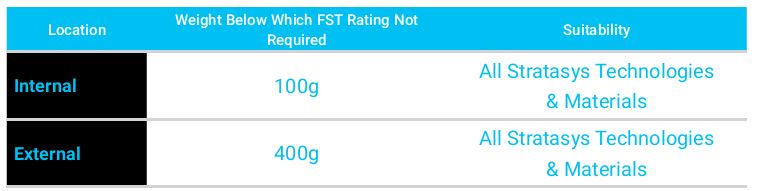
La plupart des problèmes de fabrication disposent d’une forme de solution, mais l’efficacité et l’élégance de ces solutions varient considérablement. L’impression additive se classe sans aucun doute parmi les solutions « élégamment efficaces ». Sa capacité à offrir à GWR un moyen rapide, efficace et performant de recycler les trains en est une preuve manifeste. Le choix des bons matériaux et la possibilité de créer des pièces rapidement, sans les contraintes habituelles de fabrication, ont fait toute la différence, tout comme cela a été le cas pour de nombreuses autres entreprises novatrices telles que GWR.
Vous aussi, profitez des avantages de la fabrication additive pour transformer vos projets et optimiser vos processus. Que vous cherchiez à améliorer l’efficacité de votre production, à réduire les coûts ou à innover dans vos conceptions, notre équipe d’experts est prête à vous accompagner. Contactez-nous dès aujourd’hui pour explorer ensemble comment l’impression 3D peut révolutionner votre entreprise et répondre à vos besoins spécifiques.