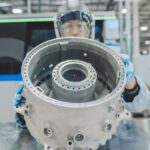
Un départ en vol : Le parcours de la fabrication additive de GE Aerospace
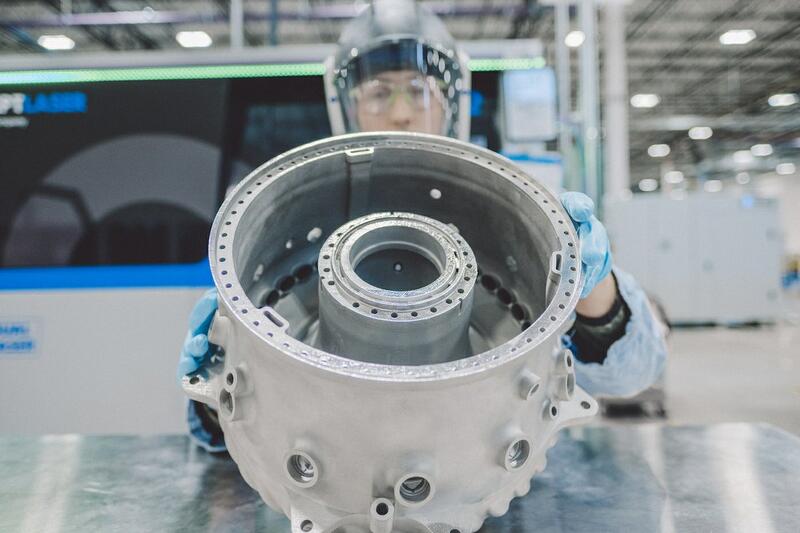
Nous sommes en août 2016 et l’armée américaine a accordé à GE et à la société Advanced Turbine Engine Company, une coentreprise entre Honeywell et Pratt & Whitney, des contrats de 24 mois pour soumettre leurs moteurs proposés pour les hélicoptères militaires Boeing AH-64 Apache et Sikorsky UH-60 Black Hawk à une revue préliminaire de conception. En avril 2018, il est temps de passer aux démonstrations.
L’une des principales exigences du contrat, en plus d’augmenter la puissance de, disons, 50% et de réduire la consommation de carburant de, disons, 25%, était que les nouveaux moteurs s’intègrent dans les structures existantes. Pour valider avec succès la conception de son moteur et son ajustement correct dans les hélicoptères, GE a utilisé son laboratoire d’impression 3D de polymères au sein de son Centre de technologie additive (ATC) à Cincinnati pour développer un prototype imprimé à la taille réelle de son moteur T901.
Le moteur T901 de GE comprend de nombreuses avancées technologiques qui ont été démontrées avec succès lors de cette phase d’essais en laboratoire et sur moteur, ce qui a conduit l’armée américaine à accorder à GE un contrat de 517 millions de dollars qui lui permettra d’utiliser à nouveau sa capacité de fabrication additive de métaux. L’ingénierie et la fabrication de plusieurs composants métalliques additives du moteur T901 progressent bien. Le premier moteur de développement a été mis en marche en 2022 et les premiers moteurs d’essai en vol doivent maintenant être livrés à l’automne 2023.
En mars, lors d’une visite du ATC de GE Aerospace à Cincinnati, TCT a obtenu des informations sur les applications de fabrication additive T901 pour les plates-formes Apache et Black Hawk. Voici le parcours de la fabrication additive de GE Aerospace, application par application.
La première pièce approuvée par la FAA et imprimée en 3D
« Tout a commencé avec cette pièce », c’est ainsi que GE aime parler de sa buse de carburant LEAP imprimée en 3D. Et bien que cette buse – avec sa réduction de poids de 25% et son augmentation de l’efficacité de 30% – ait donné le coup d’envoi du voyage de fabrication additive de l’entreprise, c’est le développement rapide du boîtier de capteur T25 du GE90 qui a donné naissance à la première pièce approuvée par la FAA (Federal Aviation Administration) il y a huit ans.
La pièce devait subir une refonte, alors le ATC a été chargé d’utiliser la fabrication additive pour développer et industrialiser rapidement une nouvelle solution. Dix pièces ont été consolidées en une seule, et 12 unités ont été imprimées en une seule construction. Environ 400 de ces composants ont été fabriqués et installés sur les moteurs GE90-94B.
Plus de 180 000 buses de carburant LEAP imprimées en 3D ont maintenant été expédiées, avec 1 000 unités fabriquées chaque semaine dans l’usine de fabrication d’Auburn de GE.
« Nous devions le faire rapidement et être en mesure d’itérer rapidement, c’est pourquoi nous avons utilisé l’impression 3D », déclare Chris Philp, responsable du site ATC.
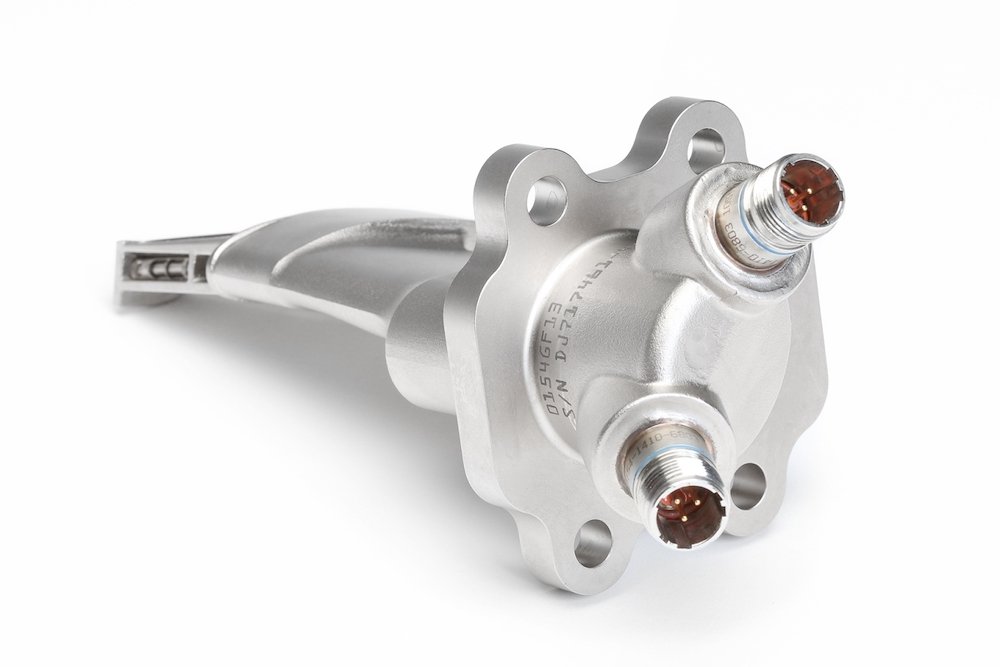
Échangeur thermique
Après avoir amélioré les boîtiers de capteur T25, des concepts de conception similaires ont été rapidement appliqués aux échangeurs de chaleur, avec des réductions significatives de l’assemblage, de la taille, du poids et du coût des pièces. Sur le moteur GE9X, par exemple, GE a incorporé un échangeur thermique en aluminium F357 fabriqué sur la Concept Laser M2, qui est 40% plus léger. Il regroupe également 163 composants traditionnellement fabriqués en une seule pièce imprimée.
« Un échangeur de chaleur [conventionnel] a de nombreux tubes soudés ensemble et nous l’avons imprimé en une seule pièce solide », explique Philp. « Il est donc beaucoup plus durable et présente moins de risques de défaillance. »
Nous sommes en août 2016 et l’armée américaine a accordé à GE et à la société Advanced Turbine Engine Company, une coentreprise entre Honeywell et Pratt & Whitney, des contrats de 24 mois pour soumettre leurs moteurs proposés pour les hélicoptères militaires Boeing AH-64 Apache et Sikorsky UH-60 Black Hawk à une revue préliminaire de conception. En avril 2018, il est temps de passer aux démonstrations.
L’une des principales exigences du contrat, en plus d’augmenter la puissance de, disons, 50% et de réduire la consommation de carburant de, disons, 25%, était que les nouveaux moteurs s’intègrent dans les structures existantes. Pour valider avec succès la conception de son moteur et son ajustement correct dans les hélicoptères, GE a utilisé son laboratoire d’impression 3D de polymères au sein de son Centre de technologie additive (ATC) à Cincinnati pour développer un prototype imprimé à la taille réelle de son moteur T901.
Le moteur T901 de GE comprend de nombreuses avancées technologiques qui ont été démontrées avec succès lors de cette phase d’essais en laboratoire et sur moteur, ce qui a conduit l’armée américaine à accorder à GE un contrat de 517 millions de dollars qui lui permettra d’utiliser à nouveau sa capacité de fabrication additive de métaux. L’ingénierie et la fabrication de plusieurs composants métalliques additives du moteur T901 progressent bien. Le premier moteur de développement a été mis en marche en 2022 et les premiers moteurs d’essai en vol doivent maintenant être livrés à l’automne 2023.
En mars, lors d’une visite du ATC de GE Aerospace à Cincinnati, TCT a obtenu des informations sur les applications de fabrication additive T901 pour les plates-formes Apache et Black Hawk. Voici le parcours de la fabrication additive de GE Aerospace, application par application. La première pièce approuvée par la FAA et imprimée en 3D
« Tout a commencé avec cette pièce », c’est ainsi que GE aime parler de sa buse de carburant LEAP imprimée en 3D. Et bien que cette buse – avec sa réduction de poids de 25% et son augmentation de l’efficacité de 30% – ait donné le coup d’envoi du voyage de fabrication additive de l’entreprise, c’est le développement rapide du boîtier de capteur T25 du GE90 qui a donné naissance à la première pièce approuvée par la FAA il y a huit ans.
La pièce devait subir une refonte, alors le ATC a été chargé d’utiliser la fabrication additive pour développer et industrialiser rapidement une nouvelle solution. Dix pièces ont été consolidées en une seule, et 12 unités ont été imprimées en une seule construction. Environ 400 de ces composants ont été fabriqués et installés sur les moteurs GE90-94B.
Plus de 180 000 buses de carburant LEAP imprimées en 3D ont maintenant été expédiées, avec 1 000 unités fabriquées chaque semaine dans l’usine de fabrication d’Auburn de GE.
« Nous devions le faire rapidement et être en mesure d’itérer rapidement, c’est pourquoi nous avons utilisé l’impression 3D », déclare Chris Philp, responsable du site ATC.
Échange Boîtier de capteur T25, première pièce approuvée par la FAA et imprimée en 3D de GE. Le capteur fournit des mesures de pression et de température pour le système de contrôle du moteur GE90. Boîtier de capteur T25, première pièce approuvée par la FAA et imprimée en 3D de GE. Le capteur fournit des mesures de pression et de température pour le système de contrôle du moteur GE90. Échangeurs de chaleur
Après avoir amélioré les boîtiers de capteur T25, des concepts de conception similaires ont été rapidement appliqués aux échangeurs de chaleur, avec des réductions significatives de l’assemblage, de la taille, du poids et du coût des pièces. Sur le moteur GE9X, par exemple, GE a incorporé un échangeur de chaleur en aluminium F357 fabriqué sur le Concept Laser M2, qui est 40% plus léger. Il regroupe également 163 composants traditionnellement fabriqués en une seule pièce imprimée.
« Un échangeur de chaleur [conventionnel] a de nombreux tubes soudés ensemble et nous l’avons imprimé en une seule pièce solide », explique Philp. « Il est donc beaucoup plus durable et présente moins de risques de défaillance. »
Une nouvelle application
Après avoir prouvé à la FAA qu’ils pouvaient fabriquer de manière additive des pièces d’avion fiables, GE était encouragé. En s’engageant dans sa plate-forme de moteur GE9X, GE a vu l’opportunité d’utiliser l’impression 3D dans son nouveau moteur. L’équipe a décidé d’appliquer la fabrication additive à un composant de passage d’écoulement, qui ne pouvait pas être produit conventionnellement dans les contraintes du moteur.
Ainsi, GE a conçu un composant d’inducteur cyclonique qui utilise les forces centrifuges pour « dévier les particules de poussière vers l’extérieur de la voie d’écoulement, avant d’être aspirées dans le flux principal, améliorant ainsi la durabilité », selon Philp.
GE était si confiant dans la conception additive de ce composant qu’ils ont développé leurs moteurs en tenant compte de la pièce avant l’obtention de la certification de la FAA. Ce composant est fabriqué sur le système Concept Laser M2 en alliage de cobalt-chrome et a été regroupé en une seule pièce à partir de 13 pièces. On dit aussi qu’il est deux fois plus durable qu’auparavant. Huit inducteurs cycloniques imprimés en 3D sont installés sur chaque moteur GE9X.
Il est prévu de remotoriser environ 1.300 hélicoptères Sikorsky UH-60 Black Hawk et 600 hélicoptères Boeing AH-64 Apache. Chaque hélicoptère possède deux moteurs.
Pales de turbine basse pression
Comme déjà mentionné dans le magazine TCT, GE connaît également un succès avec la technologie Arcam Electron Beam Melting (EBM). Un total de 228 pales de turbine basse pression sont fabriquées de manière additive sur l’Arcam EBM A2X en alliage de titane aluminure pour chaque moteur GE9X. Ces composants contribuent à une amélioration de l’efficacité énergétique de 10% et sont 50% plus légers que leurs homologues fabriqués traditionnellement. En raison du processus EBM qui élève la température à l’intérieur de la machine à 1 200 °C, de plus petits gradients thermiques sont générés et les composants subissent moins de contraintes résiduelles pendant la fabrication. Un moteur – tolérance zéro aux défaillances
GE a également utilisé l’impression 3D sur son moteur Catalyst pour l’avion monomoteur Cessna Denali. Et c’est là que l’application de la fabrication additive par GE devient plus grande et plus complexe.
« Nous avons vraiment adopté une approche nouvelle pour concevoir ce moteur. C’est le prochain niveau », déclare Philp.
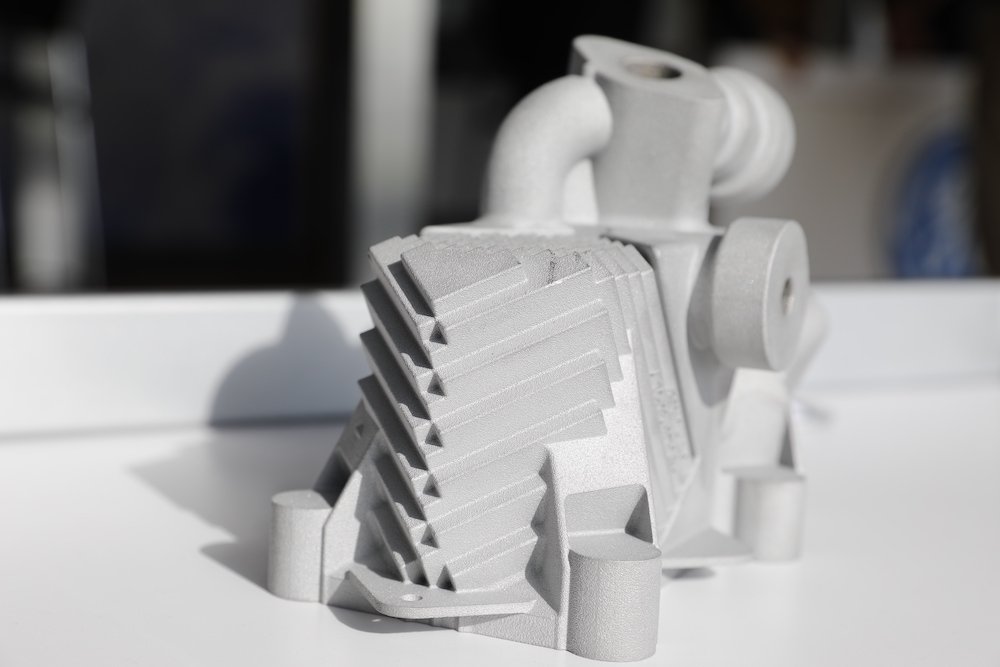
Échangeur thermique de turbopropulseur avancé de fabrication additive pour le turbopropulseur Catalyst installé sur le Cessna Denali
Dans la fabrication additive des composants du moteur turbopropulseur, GE a incorporé des profils aérodynamiques intégrés dans l’intérieur des composants du moteur pour améliorer les performances. On dit que le moteur brûle jusqu’à 20% de carburant en moins et fournit 10% de puissance supplémentaire par rapport à d’autres moteurs de la même catégorie. Parmi les pièces imprimées pour le moteur Catalyst, on trouve un échangeur de chaleur avancé pour turbopropulseur, un boîtier d’échappement et un composant en forme de C.
Châssis central T700/CT7
« C’est l’une des pièces les plus difficiles à fabriquer, et nous la fabriquons depuis 35 ans », remarque Philp à propos du châssis central CT7.
GE a créé un prototype additive du châssis central CT7, en se concentrant une fois de plus sur la consolidation des pièces. Une des opportunités d’économie de poids qu’elle avait identifiée était de regrouper les pièces pour pouvoir supprimer les brides, les écrous et les fixations, afin d’alléger le poids et d’éliminer la « soudure, le brasage et l’assemblage très complexes » des pièces. Dans le développement de ce prototype, qui a ensuite été validé sur un moteur de développement, GE a utilisé autant que possible l’impression 3D, avec des performances dépassant les attentes des itérations précédentes du moteur.
Philip suggère que le travail réalisé pour fabriquer de manière additive des composants plus grands et plus complexes tels que le châssis central CT7 a aidé l’entreprise à remporter le contrat T901, dans le cadre duquel GE a actuellement imprimé et testé des composants de fabrication additive destinés à la qualification et aux essais en vol du moteur.
« Nous utilisons les leçons apprises, ces connaissances [des projets précédents], pour dire ‘peut-être sommes-nous allés un peu trop loin, réduisons un peu’. Ce que vous voyez ici, ce sont tous des composants pour de nouveaux moteurs, et c’est vraiment là que nous obtenons le plus d’avantages de l’impression 3D », déclare Philp. « Ce n’est pas seulement dire que je peux remplacer cette pièce dans un moteur – ce boîtier de capteur était une histoire distincte – lorsque vous commencez à concevoir le moteur comme un système, avec tous les avantages de l’impression 3D, c’est là que vous obtenez des performances, un gain de poids et des économies de carburant. »
Source: TCT Magazine