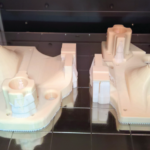
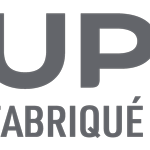
UPSA révolutionne la fabrication pharmaceutique avec l’impression 3D : une avancée technologique majeure pour l’innovation
UPSA, une entreprise pharmaceutique produisant plus de 340 millions de boîtes de médicaments chaque année, doit son succès à une remarquable famille de médecins.
C’est en 1935 que le Dr. Camille Bru fonde UPSA (Union de pharmacologie scientifique appliquée) en France, après avoir découvert que certains médicaments étaient plus efficaces lorsqu’ils étaient administrés avec de l’eau gazeuse. Cette découverte conduisit au développement des comprimés effervescents, un véritable tournant dans la recherche et la production pharmaceutiques.
UPSA est désormais détenue par Bristol-Myers Squibb, mais comme l’explique Mathieu Dumora, responsable de projets au service de support technique et infrastructure, la compagnie est toujours très attachée à ses traditions.
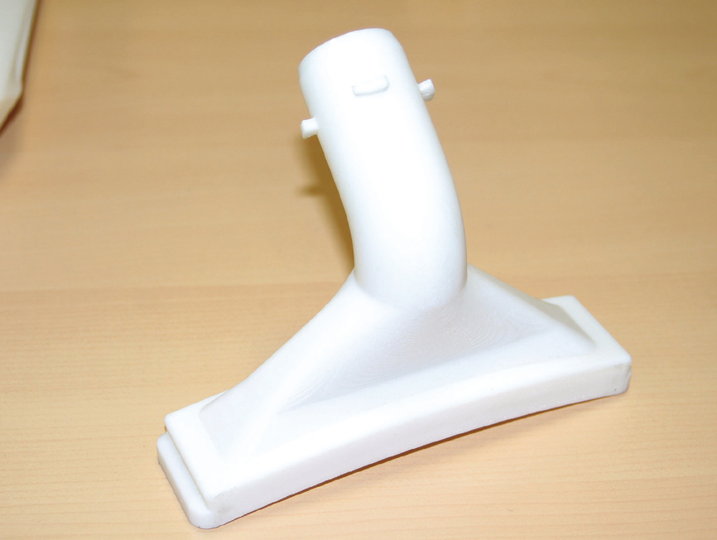
M. Dumora explique : « Il y a plusieurs années, nous avons réalisé que tout notre savoir-faire était entre les mains de nos techniciens les plus vétérans ». « Or, le nombre de jeunes susceptibles d’acquérir les compétences nécessaires diminuant, il nous fallait trouver une nouvelle approche pour notre outillage et notre atelier interne. Nous étions également limités quant aux types de pièces que nous pouvions réaliser par nous-mêmes avec nos technologies de production traditionnelles. »
UPSA effectue un suivi régulier des avancées technologiques afin d’identifier celles qui pourraient avoir un impact sur son activité. C’est ainsi qu’une analyse de l’impression 3D et de la fabrication additive lui fit sentir que l’adoption de cette technologie pourrait facilement l’aider à réduire ses coûts de fabrication et ses stocks de pièces de rechange.
« Nous avons réalisé qu’en utilisant des pièces imprimées en 3D, nous pourrions diminuer leur poids de 70 %, ce qui réduirait l’usure des machines, donc leur longévité, et aurait un grand impact sur la productivité. », commente M. Dumora.
Selon lui, l’emploi de la technologie FDM® et de la Fortus 450mc™ n’a pas seulement revitalisé leur atelier interne, mais encore stimulé la créativité dans l’ensemble de la compagnie. « Chez UPSA, certains d’entre nous ne savaient même pas que nous avions un atelier », explique-t-il. « Aujourd’hui, des gens de tous les départements nous proposent leurs idées, ou viennent nous voir avec des problèmes spécifiques à résoudre. »
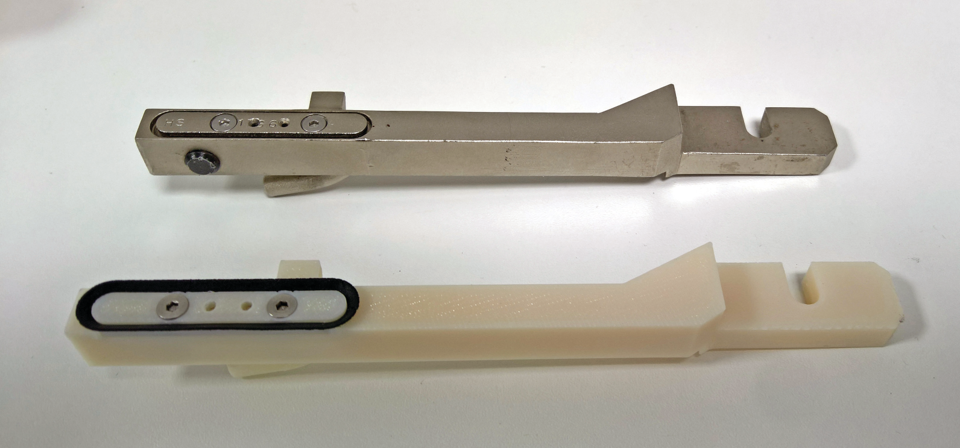
95% de réduction des coûts avec une seule pièce
Après l’adoption de l’impression 3D, la priorité était le remplacement des pièces critiques des machines, et sur ce point, la Fortus 450mc fit rapidement ses preuves. UPSA ne fait pas que développer des médicaments, elle assure aussi leur fabrication et leur conditionnement. L’une des pièces de ses équipements de fabrication utilise un lourd bras en acier moulé pour saisir et aspirer une boîte en carton dans laquelle sont insérés les blisters.
« Ces bras étaient lourds. Ils pouvaient parfois se déformer, tomber en panne et casser la machine », précise M. Dumora. « L’utilisation d’un bras imprimé en 3D est plus sûre, le matériau d’impression 3D ABS-M30i™ peut récupérer sa forme s’il se fausse. Et s’il se casse, il peut être rapidement remplacé par impression pour un coût réduit. C’est une amélioration considérable par rapport à la pièce en acier, très coûteuse. En une seule année, nous avons produit 55 de ces pièces et réalisé une économie de 95 % sur chacune d’elles. »
La fabrication additive remplace les inspections, onéreuses et chronophages
UPSA a également imprimé en 3D un dispositif destiné à améliorer la sécurité du bouchon de son Efferalgan (paracétamol) pédiatrique. Les bouchons du fournisseur contenaient des particules qui risquaient de contaminer le médicament. Une inspection visuelle, onéreuse et chronophage, devait être réalisée, à la fois par UPSA et par le fournisseur.
« Nous avons créé une équipe à partir de membres des départements de qualité, de maintenance et de production, pour développer un système spécial qui aspire et souffle de l’air afin d’éliminer les particules », explique M. Dumora. « Nous avons analysé l’air aspiré, et même placé des particules dans les bouchons pour tester son efficacité. La fabrication additive nous a permis de réaliser cette solution par nous-mêmes, et de l’améliorer rapidement grâce à la mise en œuvre de plusieurs itérations pour un coût raisonnable. Et cela nous a permis de mettre un terme aux inspections visuelles qui étaient onéreuses et chronophages. »
Des économies considérables, grâce à des supports de caméra imprimés en 3D
Un autre exemple de conception créative et pratique est la construction de supports de caméra sur la chaîne de production. UPSA applique sur ses emballages un code de suivi et de traçage. Et pour veiller à ce que ces informations vitales soient correctement imprimées, une caméra est installée au-dessus de chaque machine.
Un ingénieur de conception d’UPSA a ainsi utilisé la Fortus 450mc pour concevoir le support et en imprimer 22 unités en 3D, une pour chaque machine. Avant cette innovation, le montage de 27 pièces
était nécessaire. La nouvelle conception n’en requiert que deux, ce qui représente une réduction significative du temps et du coût de production.
« Depuis que nous l’avons, nous avons élargi les domaines d’application de notre Fortus 450mc », affirme M. Dumora. « Nous l’avons utilisée pour fabriquer de nouvelles pièces et des pièces de rechange, améliorer la chaîne de fabrication et créer des pièces personnalisées et des prototypes fonctionnels nous permettant d’accélérer le processus de prise de décision. En réalité, le résultat positif immédiat est que dès la première année où nous avons implanté cet équipement, nous avons largement récupéré notre
investissement. »
« Notre imprimante 3D est à la fois fiable et simple à utiliser. Il est incroyable de voir une machine travailler sans interruption, sans aucune défaillance, et produire des pièces à la finition parfaite. Dans
un premier temps, nous avions une certaine réticence à l’utiliser pour de gros volumes, car nous ne connaissions pas encore sa fiabilité technique et la constance de ses performances. Mais elle s’est avérée être une véritable bête de somme, capable de fonctionner nuit et jour pendant 15 jours, pour fournir des résultats fantastiques », souligne M. Dumora.
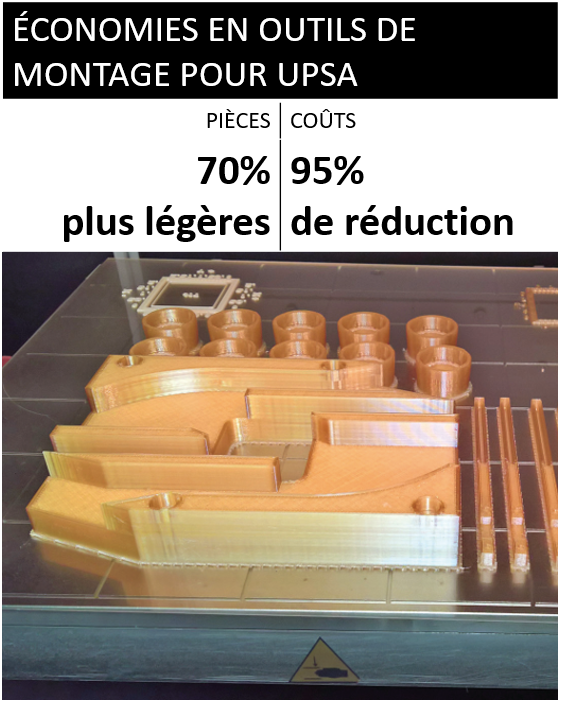
Source: Stratasys